Introduction
Have you ever wondered what happens when a customer returns the product? Does it break the supply chain management? Returns are just part and parcel of online shopping these days. So, how can you get to handle reverse logistics anything from customer returns, and warranty claims to product recalls?
The average e-commerce return rate is estimated to be 20-30% which in turn leads to a cost of $400 billion annually in the United States. Most of the returns are due to quality issues or the wrong product delivered.
Let’s explore how to untie the complexities of reverse logistics and master the intricacies with effective strategies.
What is reverse logistics?
In simpler terms, reverse logistics is the opposite of traditional or forward logistics which focuses on the goods movement back from the customer to the manufacturer or supplier. It involves returns, repairs, recycling, or disposal.
Imagine when a customer returns a product due to dissatisfaction. The average cost of processing a return is estimated to be between $10 and $20. As you must deal with these challenges, it is important to improve reverse logistics.
Stages of Reverse Logistics
First, let’s learn about the stages of reverse logistics which involves managing returns through multiple stages. It is a step-by-step process that deals with the movement of returned goods from customer to manufacturer.
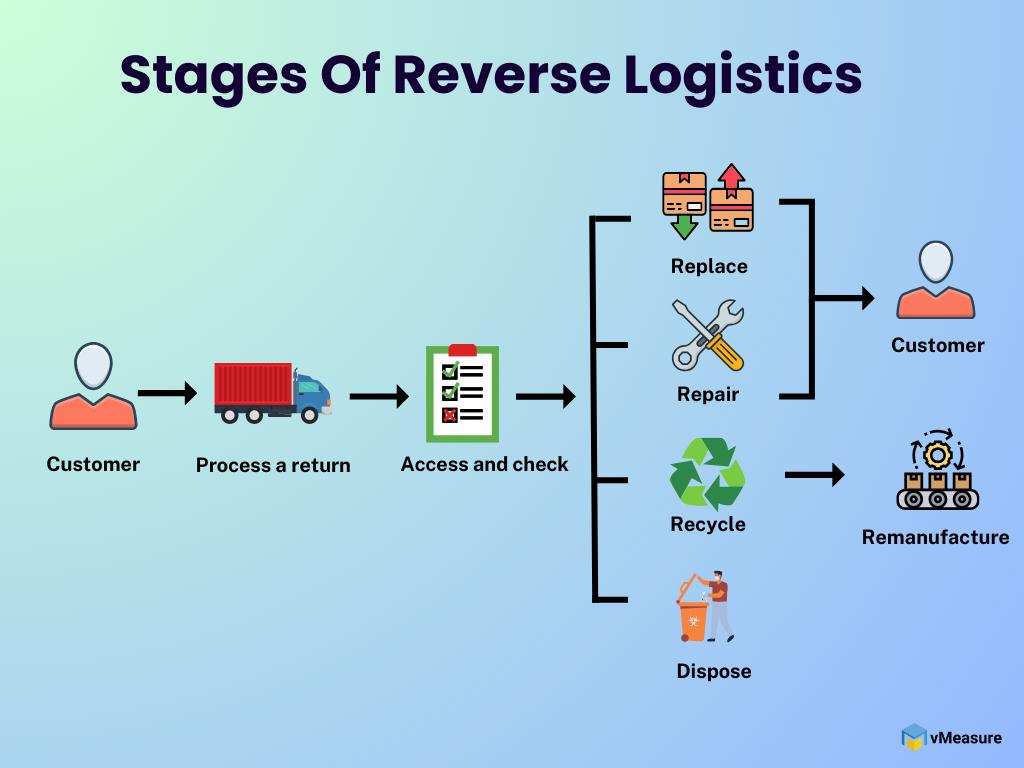
1. Process a return: How much weight does the freight have about its size?
When a return is initiated by a customer, the product is assessed and picked by the logistics partner and sent to the manufacturer or supplier
2. Assess and check
Upon receiving the returned product, it is checked for its condition and whether you can resell, repair, refurbish, or dispose.
3. Keep return or replace
If the product is returned due to a wrong size issue, it can be moved to the inventory for reselling. If the customer has initiated a replacement, then the specific product is shipped to the customer.
4. Repair
If the return is due to warranty claims. It is checked if it can be repaired or refurbished and sent to the discount channel.
5. Recycle
If the goods are completely damaged, they are validated if all or a few parts of the product can be recycled and brought into production again.
6. Dispose
If the goods cannot find a way back into the supply chain, they can be completely disposed of to align with environmental sustainability.
Strategies To Improve Reverse Logistics
As we are aware of the different stages in reverse logistics. Let’s throw some light on how to improve it. Like traditional supply chain planning, procedures for reverse logistics should be developed with an emphasis on controlling costs and retaining customer loyalty.
#1 Sorting the Returned Goods
Begin the sorting process by categorizing returned items based on their condition, reason for return, and resale potential. Proper sorting allows rapid identification of resalable items, which can be quickly restocked and returned to the sales cycle. Additionally, identifying the products that require further inspection, refurbishment, or disposal reduces unnecessary transportation costs.
#2 Invest in Technology
Automation is a transformative force in reverse logistics, automating repetitive tasks
and streamlining processes, improves efficiency and accuracy. Using the Internet of Things (IoT) can open a lot of opportunities to elevate processes, like integrating with sorting systems can
classify returned goods based on condition, marketability, and disposition, while integrating with the cartonization software, aids in finding the right package for the product as most the product
returns are due to package issues.
#3 Strategic Inventory Management
Strategic inventory management goes beyond handling returns; it’s about actively enhancing the reverse logistics process to seize opportunities for better efficiency. Using dynamic inventory adjustment, which updates stock levels as returned items move through the process, helps make quick adjustments and reduces holding costs.
#4 Continuous Improvement Through Data Analysis
Keep track of return rate per item basis. This can guide the volume of products returned. If a certain item is returned more often than others, it signifies the low quality or product packaging. The return cost should also be included in the financial planning and driving down on return cost can have a larger impact on your bottom line. Integrating supply chain management software supports in making determinations and valuable reports.
#5 Collaborate with Partners
Establish transparent communication channels with partners to facilitate seamless information exchange. Work collaboratively to standardize returns procedures across the supply chain. Consider working with more regional final mile, white glove, and LTL firms. Often, they will provide better service at a better rate than the national carriers in specific regions. This supports contributing to a more sustainable and resilient supply chain.
#6 Customer Communication and Feedback
Effective customer communication and feedback mechanisms are indispensable components of a successful reverse logistics strategy. Consider offering flexible return options, such as extended return windows or hassle-free exchanges, demonstrating a commitment to customer-centric policies. Also, include a brief survey link in post-return communication, seeking feedback on the overall returns experience and areas for enhancement. These implementations can turn returns into opportunities for positive engagement.
Benefits of reverse logistics
Customer Satisfaction
The core value of reverse logistics is valuing customers. It helps to build customer loyalty and improve sales. With the rapid increase in e-commerce sales, it’s becoming easier for customers to switch between competitors following a bad experience in return issue. Amazon and Walmart’s easy return policy has become nearly necessary for every e-commerce companies. By analyzing return data and customer feedback, businesses can refine their return policies to strike a balance between customer satisfaction and cost efficiency.
Sustainability
Engaging in reverse logistics operations, such as repairing, refurbishing, repacking, and
recycling holds the potential to reduce a company’s environmental, social, and economic footprint. Simultaneously, these activities can contribute to heightened profitability and improved asset utilization for the company. By embracing practices that extend the life cycle of products and minimize waste, businesses not only fulfill their environmental and social responsibilities but also unlock opportunities for economic gains and resource optimization.
Frequently Asked Questions
How to dispute a reclassification?
Reclassification of the freight happens when the LTL carrier finds a discrepancy between the freight class on the bill of lading and the actual freight class. To dispute a reclassification
- Keep the required documents like bill of lading, shipment details, original classifications, etc.
- Review the NMFC guidelines to ensure that your shipments have been correctly classified.
- Pay attention to the reason for reclassification. Often reclassification happens when there is a discrepancy between the item shipped and the initial information provided. Make sure to provide the updated information.
- Discuss and seek help regarding reclassification from your carrier or freight broker.
How does a change in freight class impact the shipping cost?
Consider you have a shipment of durable, car accessories and you have classified the shipment as class 65. However, after revaluation, you figured it out that these parts can be classified as under class 60 because they are denser and stowable.
- As you move the freight class from 65 to 60, your shipping cost decreases as lower-class shipments are generally less expensive.
- The reduction in freight class means you’ll pay a lower rate for the same weight, leading to cost savings.
Are freight classes universal?
Freight classes are not universal; rather, they are specific to the National Motor Freight Classification (NMFC) system used in the United States for less-than-truckload (LTL) shipments. However, there are a few exceptions.
1. Some carriers may have their own proprietary freight classification system.
2. Some carriers may offer different freight class discounts based on their shipments like high volume or certain types of commodities.
Which freight class is the cheapest and why?
Freight class 50 is the cheapest because commodities that are assigned to freight class 50 are high in density, have a low value, and have less risk in handling. As a result, carriers can ship these commodities more efficiently and at a lower cost.
What is freight class 60?
Freight class 60 is a relatively low freight class that weighs between 30 to 35 lbs per cubic foot. The goods in this classification are not extremely heavy, but they are denser than those classified under lower classes. Freight class 60 items may have moderate stowability requirements and handling characteristics. They predominantly contain car accessories, car parts, etc.
Conclusion
In a nutshell, improving reverse logistics goes beyond mere return management; it involves adopting strategies that transform challenges into opportunities. As businesses align with customer expectations, streamline processes, and prioritize sustainability, they not only navigate the complexities of reverse logistics but also thrive in an evolving and competitive marketplace.
Let’s get started!
Get in touch, and our dimensioning experts can help improve your operations and skyrocket productivity by offering the first and only dimensioning as a service.